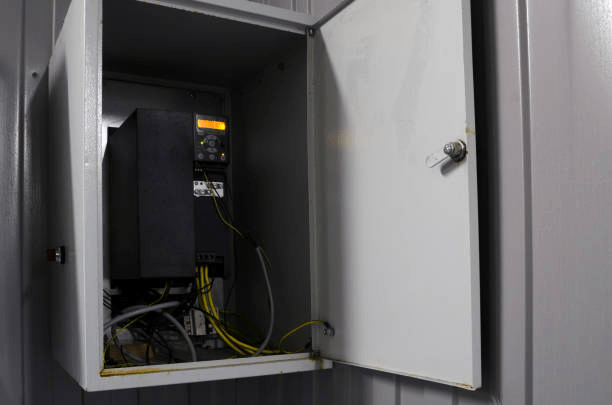
Production plants benefit from greater automation and higher production speeds. This can be seen in processing plants and even in commercial buildings, where variable frequency drives (VFD's) typically control three-phase motors in use. However, it is vital to align the VFD with the application based on four key points.
Unique Needs and Requirements of the Application
Applications of VFD’s can be grouped into three: constant torque, variable torque or constant horsepower. Matching the load characteristic to the drive is the most important task to be done in this scenario. The drive needs to equal or exceed the motor’s need for current in regular load state or in an overload.
Power Source Properties of the VFD
Once the application has been determined, the input voltage and frequency should be defined, as well as the power distribution configuration. North America usually uses ac input, but in some cases, dc is required. Low-voltage input options start at 115 V ac but could go up to as high as 690 V ac, while 50 and 60 Hz are the general input frequency ratings. While unusual, AC drives may work from dc sources, thus increasing the possibilities for alt technologies as well as applications that are more demanding. Visit this company now!
Needed Enclosure
It is important to ensure a proper enclosure because it protects the drive and lengthens its lifespan. A lot of drives are part of larger kansas city inverters automation platforms holed up in well-maintained, air-conditioned control rooms, sparing the equipment from ambient stress. Manufacturers can provide chassis or minimally protected products for this very purpose, but individual motor controllers left on their own in the field experience fluctuating conditions. Understanding the site of installation is key to the drive’s long service life.
Compatibility
There are two critical issues at this stage of the process, and one is, will feedback be required? A lot of drive applications regulate process more than speed. Drives can work with a variety of processes through embedded memory, faster processors and inputs/outputs. Get more info about inverter at https://en.wikipedia.org/wiki/Power_inverter.
These can come with a transducer attached to the drive to hold a level in a vessel with a PID/winder application in which various encoders control a number of drives for calculating necessary diameters and speeds. No matter the process type or signals being measured, they are still responsible for the drive’s output to the motor.
The other issue or question is what type of communication is required. Communication plays a crucial part in a majority of applications. In some instances, all you need is a display confirming to the operator that the process is ready. Usual communications from the drive are analog and digital outputs. In other cases, what’s needed are statistical details on the conditions the drive controls, and for this, Fieldbus communication is a good choice.